Testing and quality control
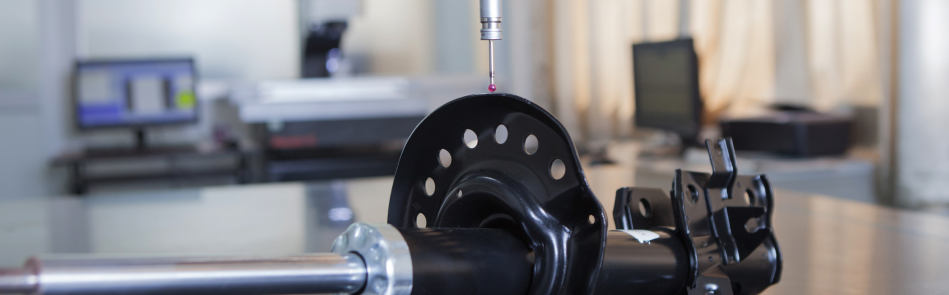
Quality control and permanent testing are one of the most important parts of any production process, especially auto spare parts, which directly affect the road safety. All TMI TATSUMI products are regularly tested at every stage of production.
TMI TATSUMI’s spare parts correspond to OE quality and often even exceed it. We are always trying to use the best property components throughout the supply chain. Each our automotive component undergoes the highest testing in order to meet the strictest and rigorous legal requirements. What is more, TMI TATSUMI’s engineers pay much attention to the choice of materials that will be used in the production process.
To offer our customers the best premium auto spare parts, we have worked out various detailed material specifications. Their aim is to control the use of unacceptable chemical components that may have an impact both on the environment and people’s health. Factories that provide TMI TATSUMI brand with auto parts have their own chemical analysis laboratories.
Our specialists devote a lot of attention to the materials that are used during the production process. One of the key characteristics is strength, especially in such product groups as bushing, silent blocks and wiper blades. The laboratories that are situated at factories investigate the quality of materials before using them in the production process. The results obtained from conducting strength tests on materials give a good indication of the quality of the material and its suitability for its intended end use.
What is more, some material can be tested for impact resistance using various methods including Izod and Charpy methods. It is common knowledge such tests are useful for comparing the relative impact resistance of different materials. This is especially important in the production of spare auto parts, which must be safe and durable.
A lot of automotive components, particularly metal, are at risk of corrosion that can lead to costly repairs and cause considerable car damage. We conduct different tests, which can help our engineers to select material types and refine designs to minimize susceptibility to the effects of corrosion. Corrosion tests typically involve the spraying of a salt solution in a testing chamber at 35°C.
Some of the auto components, for example, the elements of car’s cooling system or filtration system, are exposed to adverse weather conditions. Our testing complex is aimed at simulating different weather conditionals so that it is seen whether the produced auto components are sustainable or not.
We carry out not only testing in accordance with recognized specifications and test methods, but also try to develop our own control and quality programs. We always try to do our best for a flawless end result and bring every stage of the production process to perfection.
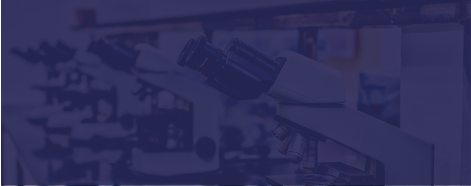