Progressive top management (JIT/KANBAN)
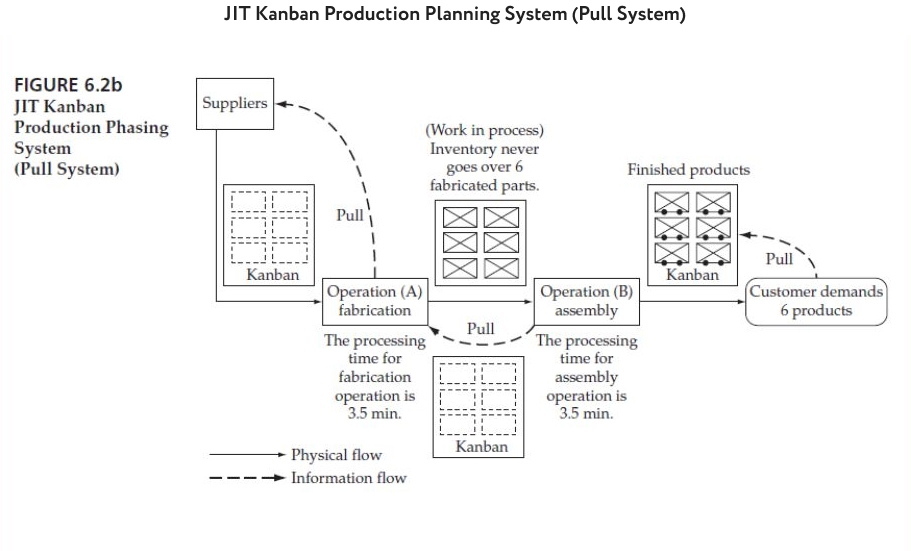
We try to achieve new goals every day. We are building trust and partnership relations between all staff in the company. We respect each employee individually. Moreover, we believe that Tatsumi owes its success to its friendly and close-knit corporate team.
To obtain the most effective results, the company's leaders combine various management and business methods at work. It is common knowledge it is highly important that the management takes the leading role in the company’s work.
One of our main methods is Just in Time (JIT) inventory management. It is a well common inventory business technique and a type of lean methodology designed to increase efficiency, cut costs and decrease waste by receiving goods only as they are really needed. JIT helps us to follow Japanese traditions as a response to the world’s limited natural resources. We care about our planet and its future because it is the future for our children. JIT has influenced many related lean inventory management techniques like IBM’s Continuous Flow Manufacturing (CFM) that is also used in our company. A JIT inventory management strategy offers a number of benefits for Tatsumi business among which are lower inventory holding costs, improved cash flow and less "dead stock" (there’s less risk of unwanted stock left sitting in the warehouse).
In addition, we pay a lot of attention to the cost reduction which is shared by both the top management and the general employees. We have a special JIT project, which chief is the head of the company. We are trying to introduce a special practice team for the greater JIT implementation. The members of the JIT practice team involve our current staff: the people from the manufacturing department, the production engineering department, the general management department and the team leaders of each process.
One of the other progressive methods that is used at our work is the KANBAN management, which bases on production and inventory control of spare auto parts connected with predicted distribution of products. This system consists of several sequential steps, which must be fully completed before moving on to the next step to ensure the best quality of the final products. The Kanban management is organized using a number of special cards in order to execute each phase. These cards or labels state what phase of the auto parts manufacturing process the products are currently in. This system perfectly copes with its tasks, it helps us to control the production process at every stage, from the selection of raw materials to the delivery of finished products to the customer.
Our main goal is to provide customers all over the world with premium, high quality and safe auto parts for all major product groups. To achieve our goals, we try to keep the inventory management process under control - efficiently compressing inventory and maintaining a standard amount of inventory using different management technics. We share the idea that inventory issues become the deciding factor when choosing the trade-off between lowering costs through inventory and increasing customer satisfaction and confidence in the company for time guarantees and urgent orders.
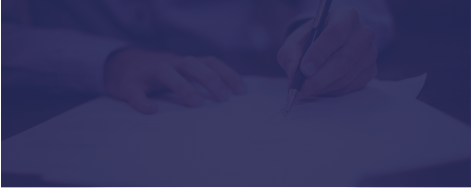